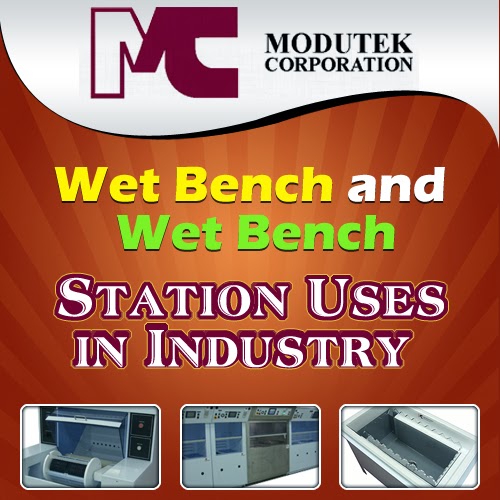
Wet benches and wet bench stations are the industry must-haves for all integrated circuit manufacturing. Semi-conductors, computer hardware, solar cells, and many medical components are all manufactured using this type of technology. They are particularly useful in clean room applications. Which wet bench or wet bench station option is chosen will vary, depending on the differing needs of a particular industry. Modutek Corporation is proud to offer a wide choice of wet bench stations. Options range from a basic manual wet bench to totally automated stations, with semi-automated models in between.
Modutek Corporation offers custom configuration of its already comprehensive line-up of production wet benches. We will work with your budget and your
specific needs to ensure that all of your requirements are met.
A Manual Wet Processing Station is a necessity in many, if not most, industries using clean rooms. Our manual wet stations are built to provide both acid and solvent application support. Our in-house design engineers will configure your wet bench station specifically to satisfy your exact application needs.
A few of the many advantages of Modutek Corporation’s Manual Wet Processing Stations include:
- Being designed to meet your unique process requirements
- Cost of ownership is lower compared to semi-automated or fully automated wet benches
- Competitive pricing for our high end manual equipment
- Meets, or exceeds, all current safety standards currently
- Designed to allow for future expansion
We want your new wet station to be an exact fit to your requirements. We encourage client input and involvement on the final design before we begin the manufacturing process. Let us review the different options offered with you, to guarantee your complete satisfaction with Modutek Corporation Wet Processing Station technology.
Semi-Automated Acid Stations can also be custom configured and manufactured according to a client’s specific needs. Many options are available. We offer in-house design and manufacture to ensure that you get all of the options you want and none of those you don’t need. The semi-automated acid stations we offer have the uniform processing and robotics you need without the greater expenses of fully automated systems. The top-of-the-line, servo-controlled robots in all of our semi-automated acid stations have 3° of freedom, which allows for precise and accurate developing, etching, and/or cleaning processes.
The Modutek Corporation Semi-Automated Stations offer these and other advantages:
- In-house software and robotics design and manufacture — no outsourcing
- SolidWorks Flow Simulation software
- SolidWorks Simulation Professional software
- Automation control using a touch screen
- Servo motor automation
Fully-Automated Acid/Base Stations offer the safety of hands-off processing. If your process necessitates complete automation, then the Modutek Corporation Fully-Automated Acid/Base Stations are the best choice. Processes from full-size 30”x 60” glass solar panels to tiny wafers can be reliably handled by our stations. Using information that your engineers specify, Modutek Corporation will configure the systems to meet your precise requirements. We never out-source so our team will be working hand-in-hand with yours to design the right wet bench station, its software, and its robotics perfect for your company’s needs.
Our Fully Automated Wafer Fabrication Equipment has these benefits:
- Everything is completed in one place - design, assembly and testing
- Our robotic and software design is also completed in-house, not outsourced
- SolidWorks Simulation Professional software
- SolidWorks Flow Simulation software
- More than 30 years experience and continuous operation
- Our goal is to provide outstanding customer support after the sale
For a quote or if you have any questions about any of our Wet Bench and Wet Bench Stations, call Modutek Corporation at 866-803-1533.